Demonstration Overview
The DoD STED Program demonstrated biobased dust suppressants for use in dust control operations at Department of Defense (DoD) and National Aeronautics and Space Administration (NASA) facilities.
Dust suppressants have been designated for Federal procurement preference by the United States Department of Agriculture (USDA) BioPreferred Program. The BioPreferred Program defines dust suppressants as
“Products formulated to reduce or eliminate the spread of dust associated with gravel roads, dirt parking lots, or similar sources of dust, including products used in equivalent indoor applications.”
The BioPreferred Program established a minimum biobased content of 85 percent for dust suppressants.
Chemical dust suppressants are applied to ground and pile surfaces to enhance their stability and reduce dust generation. In the DoD environment, excessive dust generation can present hazards to personnel and surrounding communities, transport and training, and aviation while increasing infrastructure and equipment maintenance costs. Traditional chemical dust suppression has relied on petroleum- or salt-based compounds that present environmental and corrosion risks and are not readily biodegradable. More recently, synthetic polymer and biobased products have come into use that mitigate these associated risks. Biobased dust suppressants have potential performance and Environmental, Safety and Occupational Health advantages over petroleum- and salt-based products in certain applications. Biobased dust suppressants are typically non-toxic and many are biodegradable, non-corrosive, and contain little or no Volatile Organic Compounds (VOCs).
Before these biobased products are utilized by the Military Departments and DoD Components, their performance must be proven to meet DoD requirements.
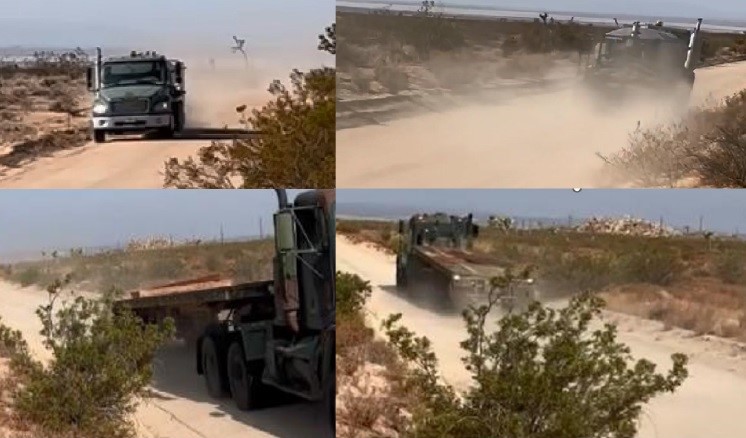
Demonstration Products*
The following products were demonstrated:
- Elimadust by Boulder Products and Services
- DustNot Bio by Momar Inc (MinTech Division)
- DustNot CG by Momar Inc (MinTech Division)
- DustAid Natural S by Momar Inc (MinTech Division)
Mention of or referral to commercial products, services, and manufacturers herein is provided for informational purposes only and does not constitute endorsement by, nor the official policy or position of, the Department of Defense (DoD), any of its Components, or the U.S. Government.
Demonstration Sites
Field demonstrations of these products were conducted at the following DoD installations and co-located federal facilities to evaluate their performance in Military and NASA operational environments and to raise awareness of biobased product availability:
- Fort Irwin/National Training Center
- Marine Corps Air Ground Combat Center Twentynine Palms
- Edwards Air Force Base (AFB)
- NASA Armstrong Flight Research Center
Demonstration Details
The demonstration plan outlined the demonstration activities that would be performed, provided an overview of the sites, summarized the selected facilities, and identified their requirements, the key performance criteria, and the products to be evaluated. Additionally, the plan noted the data to be collected, methods of analysis, and the roles and responsibilities of demonstration participants and stakeholders.
The following table contains the key performance criteria that the DoD and NASA stakeholders established to evaluate and validate that these dust suppressants met the participants’ requirements.
Demonstration Performance Criteria
Criteria | Parameters |
---|---|
Product Effectiveness |
|
Product Service Life |
|
Environmental, Health, and Corrosion Impact |
|
Ease of Application |
|
Foreign Object Debris (FOD) Avoidance |
|
Collected data included user feedback regarding the following:
- Traffic/impact on the treated surface
- Level of visually observed dust generation over the treated surface
- Wind level during observation
- Observed surface defects
- Comparison of surface traction to treatment with baseline product
- Surface disturbances or unusual weather effects impacting the treated surface
- Overall dust control compared to treatment with baseline product
- Whether treated area remained visually distinguishable from untreated areas
- Level of remaining effectiveness in mitigating dust generation
- Negative impacts to vegetation, wildlife, water quality, health, or metal components (corrosion) compared to treatment with baseline product
- Level of FOD generation compared to treatment with baseline product
Demonstration Results
Biobased dust suppressants were applied the week of 28 November 2022, following coordination with installation/facility personnel and state regulators. Their performance was then observed for six months. Treated areas/applications included:
- A 150×150-foot helipad at Bicycle Lake Army Airfield, Fort Irwin (sugar-based product)
- A vehicle trail approximately 1,500×20 feet in Logistical Support Area Santa Fe, Fort Irwin (sugar-based product)
- A 250-foot section of Manix Trail, Fort Irwin (sugar-based product)
- A 1,500-foot section of North Flank Road in the Precision Impact Range Area, Edwards AFB (glycerin-, lignin-, and soy-based products)
- Taxiway shoulders at NASA Building 703, Palmdale (sugar-based product)
- Runway endcap shoulders at the Strategic Expeditionary Landing Field (SELF), Camp Wilson, MCAGCC Twentynine Palms (sugar-based product)
Facility personnel were asked to provide product performance feedback based on the criteria and data points noted above. Overall, facility/area managers found the biobased dust suppressants to meet the identified performance requirements in all but (1) resistance to rotor downforce generated by V-22 Ospreys and (2) application over areas with less-than-optimal permeability. For all other applications, the performance of the biobased dust suppressants was comparable to or better than the baseline dust suppressant products used at the facilities. Analysis of demonstration feedback resulted in the following findings:
- Feedback indicated the demonstration biobased dust suppressants were effective at dust control and mitigation when used in road, helipad, and taxiway operations. In each of these applications, the demonstration dust suppressant products were evaluated to be effective throughout their anticipated service lives. No respondent indicated the demonstration products to be ineffective for these applications. This coincided with visual observations made by the Project Team during site closeout visits.
- Glycerin- and lignin-based dust suppressants attained their expected service life of three months. After that time, their effectiveness quickly diminished. This was exacerbated by atypically heavy convoy activities at Edwards AFB, which likely took some additional service life off the products.
- Sugar- and soy-based products outperformed their expected service life of six months, still being rated at 60% or higher effectiveness after six months.
- Although some minor surface defects occurred (one minor road surface washout, ant hill formations in the roadbed, limited cracking in taxiway shoulder surface), these were previously observed in the respective areas and did not result in any performance issues. No significant washboarding, potholing, chipping, cracking, curling, or raveling were observed. This differentiated the products from typical polymer treatment since the latter is a laminate and eventually cracks and wears away.
- When subjected to desert rainstorms, the products did not crack and fail as a result of washout, differentiating them from polymer.
- Traction remained good at all demonstration sites. None exhibited the occasional slickness characteristic of salt-based dust suppression in the region.
- Although direct observation of helipad use by respondents and the Project Team was not possible, the treated helipad was periodically used by CH-47 Chinook helicopters during the demonstration period. The surface treatment still appeared to be effective after six months and no FOD issues were reported. Because the demonstration product is not a laminate, it was not capable of locking down half-inch plus rocks, unlike polymer dust suppressants.
- Although the biobased dust suppressant used at MCAGCC Twentynine Palms succumbed to rotor wash from V-22 Ospreys after one month, the treated area returned to its natural state and did not present the sheeting FOD issues of prior polymer applications. Application of the biobased dust suppressant was topical only and it may be possible to extend service life in conjunction with V-22 use if the product is applied using a mix in method that gets significantly deeper penetration of the product into the soil surface (down to six inches).
- Application at MCAGCC Twentynine Palms was also impeded by the presence of some previously applied pavement, which prevented product penetration at the end of the runways. Because the sugar-based product was not able to cure prior to eventually evaporating, it prolonged the time coyotes were attracted to the scent and resulted in some black mold forming on the surface. These would not occur absent the lack of soil penetration resulting from the paved surface.
- The sugar-based technology combined humectant, hygroscopic, and binding properties, allowing for a level of light maintenance (e.g., light blading of the surface) without sacrificing performance. These properties also made it more resistant to damage from washout compared to polymer, and allowed it to withstand rutting and traction issues seen in prior salt-based treatments.
- The sugar-based technology performed well when applied with both reclaimed and potable water. The soy- and glycerin-based technologies were applied neat and are therefore capable of use in areas without an available water supply. The sugar- and lignin- based technologies were diluted 1:2, requiring twice the volume of water to product.
- No negative interaction was observed when the sugar-based technology was applied overtop areas previously treated with magnesium chloride or soy oil. All other areas were previously untreated or treated with only water.
- Weather during the demonstration period included the typical strong winds in the Mojave Desert and higher than average rainfall.
- The only impact to wildlife was the scent of the sugar-based technology (similar to caramel or coffee) attracting coyotes prior to full cure (typically 24 to 48 hours) in airfield areas where regular traffic did not occur to keep coyotes away. The coyotes were observed licking the surface. Some then vomited on the runways at MCAGCC Twentynine Palms, most likely due to foreign matter ingested from the surface rather than the dust suppressant itself (the main component of which is also used in animal feed). This may pose a very short-term concern for areas in which surface materials may be hazardous to coyotes or where the temporary attraction of coyotes may pose an undue threat to protected species upon which they prey. None of the demonstration areas were within critical habitat. None of the products were found to attract insects.
- No negative impacts to vegetation, water quality, or metal components (corrosion) were observed.
- The only health-related item of note was the temporary occurrence of headaches in personnel at Edwards Air Force Base’s Downfall Complex in the week following application of the glycerin-, lignin-, and soy-based technologies. Personnel at the site noted the presence of an odd odor in the parking lot (adjacent to the demonstration area) during that period, which is thought to be the cause of the headaches. None of the products exhibited an odor when opened or during application (the lignin product was not sulfonated). Nor have there been similar reports from use of the products. Thus, it is unknown whether the odor was related to the demonstration products or another cause. The odor and headaches subsided after approximately a week and did not recur.
- Products were applied using water trucks with pressurized spray bars or fans. There were no issues regarding water availability or curing time. None of the products required a curing time (i.e., site closure). Only two products (the sugar- and lignin-based technologies) had a recommended/preferred curing time (24 to 48 hours) and it was easily managed at all the sites. All products were driven on shortly after being applied without issue.
- The only temperature issue encountered was cold overnight temperatures (down to the teens and 20s) causing the sugar- and lignin-based technologies to temporarily become less flowable. This can be overcome by heating the products and can be avoided by storing materials inside insulated buildings during periods of below freezing temperatures. Temperatures did not exceed 100° Fahrenheit during the demonstration period, which would allow for twice annual application. However, if a site did want to store product during the summer, when temperatures in the Mojave exceed the 100° to 120° recommended storage temperatures, the storage facilities would need to be temperature controlled or otherwise capable of avoiding higher internal temperatures.
- Cost effectiveness is dependent on several site-specific factors and is difficult to generalize. The sugar- and lignin-based technologies are price competitive with polymer and salt products used in the region, though the cost effectiveness of the lignin product would depend on its realized service life in comparison to polymer or salt at the specific site. Although the price of the soy-technology was currently higher than that of polymer and salt products used, its strong effectiveness over a long period of time could result in life cycle costs on par or less than that of polymers and salts. The glycerin-based technology was currently more expensive than polymers or salts used in the region and had a similar service life in road applications but offers additional performance (compared to salts) and environmental benefits. The prices of soy and glycerin technologies are somewhat tied to agricultural feedstock prices and can fluctuate accordingly.
Biobased Products
The USDA BioPrefereed Catalog (https://www.biopreferred.gov/BioPreferred/faces/catalog/Catalog.xhtml) lists biobased dust suppressants and provides contact information for manufacturers.